Introduction:
In the realm of modern technology, microfluidics has emerged as a groundbreaking field with vast applications across various industries, including biomedical, chemical, and environmental sciences. Microfluidic devices allow for precise manipulation and control of tiny amounts of fluids, enabling advancements in diagnostics, drug delivery, and lab-on-a-chip systems. Behind the scenes of these sophisticated devices lies an essential fabrication technique: injection moulding. In this blog post, we will explore how injection moulding plays a pivotal role in the production of microfluidic devices, revolutionizing the field of microfluidics.
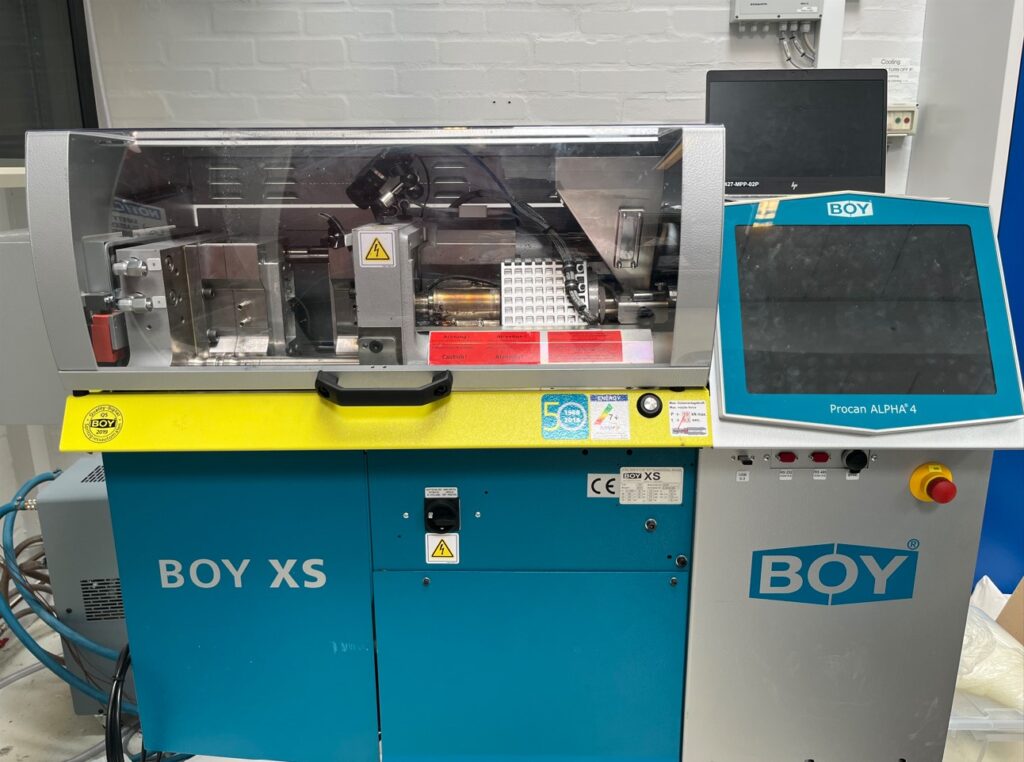
Understanding Injection Moulding:
Injection moulding is a manufacturing process widely employed in the production of plastic components and intricate parts. It involves injecting molten material, typically thermoplastics, into a pre-designed mould cavity under high pressure. Once the material cools and solidifies, the mould is opened, and the finished product is extracted. This technique enables the mass production of complex shapes with high precision and repeatability.
Benefits of Injection Moulding in Microfluidics:
- High Precision: Microfluidic devices often require intricate channels, valves, and chambers with precise dimensions. Injection moulding provides exceptional precision, allowing for the production of microfluidic components with tight tolerances. This level of accuracy is crucial for reliable fluid manipulation and experimental reproducibility.
- Scalability: With injection moulding, it is possible to produce microfluidic devices on a large scale. The ability to replicate intricate designs consistently and rapidly makes injection moulding an ideal technique for meeting the growing demand for microfluidic devices in research laboratories, medical facilities, and industrial applications.
- Material Versatility: Injection moulding offers versatility in material selection, accommodating a wide range of thermoplastics suitable for microfluidic applications. These materials exhibit desirable properties such as transparency, chemical resistance, and biocompatibility, enabling their integration into diverse microfluidic platforms.
- Cost-Efficiency: The ability to produce microfluidic devices in bulk through injection moulding significantly reduces manufacturing costs per unit. This advantage makes microfluidics more accessible for researchers, promotes commercialization, and encourages wider adoption of microfluidic technologies across industries.
Applications of Injection Moulded Microfluidics:
- Lab-on-a-Chip Systems: Injection moulding enables the fabrication of integrated microfluidic systems on a single chip. These lab-on-a-chip devices combine various functionalities, such as sample preparation, mixing, and analysis, into a compact and portable format. They find applications in point-of-care diagnostics, environmental monitoring, and personalized medicine.
- Drug Delivery Systems: Microfluidic devices manufactured through injection moulding are revolutionizing drug delivery methods. Precise control over fluid flow and the ability to design complex geometries within microchannels enable targeted drug delivery, ensuring accurate dosing and minimizing side effects.
- Biomedical Research: Microfluidic platforms have become invaluable tools in biomedical research, enabling the study of cellular behavior, organ-on-a-chip models, and high-throughput screening. Injection moulding facilitates the production of custom microfluidic devices tailored to specific research needs.
Conclusion:
Injection moulding has emerged as a key technology in the fabrication of microfluidic devices, propelling advancements in numerous fields. Its precision, scalability, material versatility, and cost-efficiency make it an ideal manufacturing process for the production of complex microfluidic components. As the demand for microfluidic devices continues to grow, injection moulding will play a vital role in enabling their widespread adoption, driving innovation, and transforming the landscape of science and technology.