As a PhD student in the SIMPPER_MedDev programme, this year has commanded me to work on multiple projects and goals, shifting constantly between ideas and mindsets. Besides my project work, there have been modules and trainings, conferences and secondments, and collaborations and co-authorings. While many people will argue that doing too many different things at the same time is counter-productive, I have learned that it can be of great benefit, but only if we learn to slow it down. People like Albert Einstein and Charles Darwin were able to discover and conceive so vastly and broadly in their lifetime because they were able to steadily move between several projects, one at a time, as the situation demanded. This is a practice that Tim Harford coined ‘slow motion multitasking’. He explained it brilliantly in his TED talk:
In short, intentional and gradual task-switching allows the subconscious mind to process prior tasks, fostering connections between seemingly unrelated topics in the background. As we practice deliberate multitasking, gradually applying insights from one task to various aspects of our work, our problem-solving abilities become more effective and efficient. While rapid multitasking hinders productivity, a slower approach may unlock the creative genius within us.
In the context of my PhD, tasks like the two training modules done in September (see the blog of Myka Mae Duran, ESR5) and the joint research performed during the secondment Christian Herrmann (ESR9) at FHNW, has allowed me to switch intentionally between different tasks. However, there was one recent example in 2023 that allowed me to gain knowledge and fresh perspectives that already supplemented the areas of my research: my secondment at Flex Precision Plastics in Hägglingen, Switzerland.
A short and focussed switch to Flex
As PhD researchers working on fundamental problems, we rarely get insight into the industries that we are trying to advance. I had the privilege of doing so in November, when I spent four weeks in each department of the company, gaining both high-level organisational insights, as well as low-level and first-hand technical experience.
Flex is a leading advanced manufacturing company with over 50 years of experience, specialising in delivering efficient and scalable solutions. They employ state-of-the-art manufacturing, particularly in industrial-scale injection moulding, collaborating with clients from design to full product life cycle.
Their focus is primarily on medical products in the healthcare sector, and they work with key industry players like Roche and Straumann, offering expertise in producing injection-moulded plastic parts for various healthcare applications. The purpose of the secondment is to gain practical knowledge of medical-grade product manufacturing, understand the supply chain, and how they ensure quality and compliance.
Since the application of my work is to produce and test rapid prototype moulds for the injection moulding of medical devices, this was the perfect opportunity for me to learn how these full-scale operations function. I saw that prototyping and sampling take place up until the serial manufacturing process is started, which allowed me to reshape the way I think and understand the problems in the lab.
It was thanks to the efficient management of my secondment programme by Tobias Meier that this was possible; and that I can now take on 2024 with the expectation of new connections and ideas to emerge.
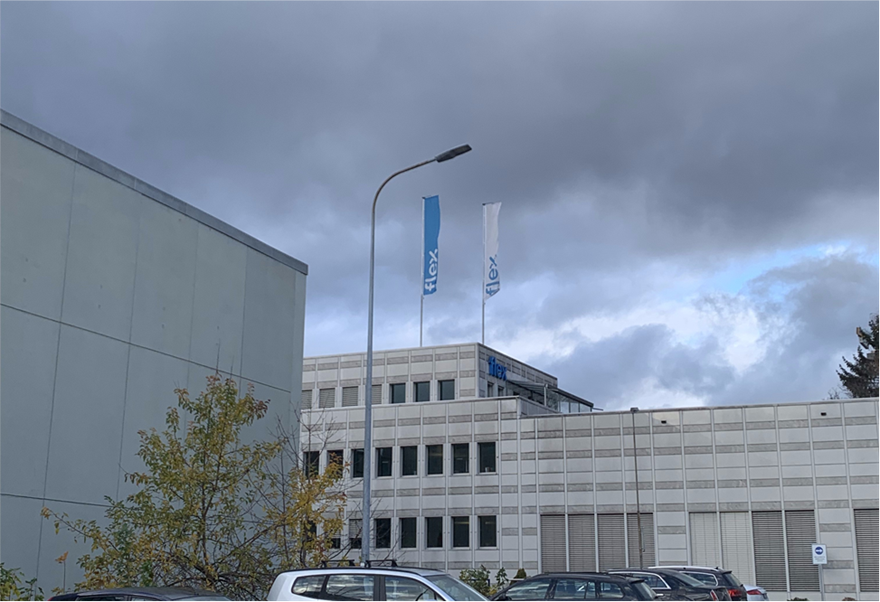